When you’re tackling a delicate welding project, there’s no room for error. Whether it’s thin metals, intricate designs, or joints that demand absolute precision, TIG welding (Tungsten Inert Gas welding) consistently proves to be the top choice.
What Sets TIG Welding Apart
If you’ve ever seen a TIG welder in action, you’ll notice right away that it’s all about precision. The method uses a tungsten electrode to create a controlled arc, which gives the welder an unmatched level of control. Unlike MIG welding, which relies on a continuously fed wire, or stick welding, which uses electrodes that burn away as you weld, TIG welding doesn’t force you to use filler material unless you want to. This level of precision makes TIG ideal for the most intricate tasks.
Another big win for TIG welding is its versatility. It works on metals like aluminium, stainless steel, and titanium—materials often used in industries like aerospace and automotive. If you’ve ever tried welding thin aluminium sheets with a MIG welder, you know how frustrating it can be to avoid warping or burn-through. With TIG welding, you can fine-tune the heat input to handle these tricky materials.
And let’s talk about the finish. TIG welders for sale produce a clean, polished weld that often needs little to no additional cleanup. That’s a huge bonus for jobs where the appearance of the weld matters, like in jewellery making, high-end automotive work, or artistic metal projects.
Why Other Welding Methods Struggle
While MIG and stick welding each have their strengths, they often fall short in delicate scenarios. MIG welding, for instance, is a great choice when speed is a priority, but it doesn’t offer the same precision as TIG. The filler wire used in MIG can make it tricky to get a seamless joint, especially when you’re working with thin or fragile materials.
Stick welding is tough and reliable, but it’s better suited for heavy-duty jobs. Its lack of finesse and the rougher welds it produces make it a poor match for fine, detailed work. For projects that demand clean, precise results, these methods can be limiting.
TIG welding fills the gap by giving you the control and accuracy that MIG and stick just can’t match. It’s slower and requires more skill, but the quality of the results makes the extra effort worthwhile.
Tackling Thin Materials with Confidence
Thin materials are notoriously difficult to weld. Apply too much heat, and you risk burning through or warping the material. Use too little, and the weld won’t hold. TIG welding solves this problem with its precise heat control.
Take stainless steel as an example. This material is prone to distortion under high heat, but TIG welding lets you fine-tune the amperage to avoid problems. The same goes for aluminium, which can crack or weaken with improper welding techniques. TIG’s ability to produce a smooth, even weld without overheating the material is a huge advantage here.
Another benefit is the inert gas shield (typically argon) used in TIG welding. This protects the weld area from contaminants, ensuring a strong, clean bond. For delicate jobs, this attention to detail is essential.
Perfect for Intricate Projects
It’s not just thin materials that benefit from TIG welding—it’s also about the complexity of the job. Whether you’re repairing a cracked pipe, welding tiny components, or creating a detailed piece of metal art, TIG welding offers the precision and flexibility to get it right.
Let’s say you’re working on a piece of jewellery. The connections need to be seamless, not just for durability but for appearance. MIG or stick welding simply wouldn’t cut it here. With TIG, you have the fine control needed to create joints that are both strong and beautiful.
This level of detail is why TIG welding is used in industries like aerospace and electronics, where the margin for error is virtually zero. Even hobbyists working on custom bike frames or sculptures can take their projects to the next level with TIG welding.
The Skill Behind the Method
If TIG welding is so effective, why doesn’t everyone use it for every job? The answer comes down to skill and time. TIG welding isn’t as beginner-friendly as MIG or stick welding. It requires a steady hand, a good eye for detail, and plenty of practice.
For instance, TIG welders often use a foot pedal to control the heat while they work, which adds a layer of complexity. It’s not just about moving the torch—it’s about balancing heat, filler material, and movement all at once. That level of control is what makes TIG welding so effective, but it’s also why it takes time to master.
Where TIG Welding Shines
TIG welding isn’t just for a specific niche—it’s widely used across industries. Here are some of the areas where it truly excels:
- Aerospace – Welding lightweight but strong metals like titanium and aluminium.
- Automotive – Perfect for custom bodywork, exhaust systems, and fine repairs.
- Jewellery Making – Creates flawless connections in intricate designs.
- Medical Equipment – Produces clean, sanitary welds for instruments and tools.
- Artistic Metalwork – Offers the precision needed for unique, creative pieces.
Its versatility makes TIG welding an invaluable tool, whether you’re a professional in a high-tech industry or a hobbyist working on personal projects.
Precision You Can Count On
TIG welding isn’t just another option—it’s the gold standard for delicate jobs. Whether you’re crafting a detailed design, welding thin materials, or striving for a perfect finish, TIG welding gives you the control you need to achieve exceptional results every time.
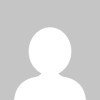