Improving tool life by actively monitoring processes is essential for a successful production. Identifying the cause of your tool’s degradation can help minimize damage and maximize performance.
Identify Tool Wear Effects
Detecting tool wear can be challenging, especially in machines with high production rates. Recognizing the early warning signs of tool failure is essential for maximizing productivity and reducing scrap parts or faulty products.
The most common symptoms of a problem with a machine are:
- Irregular cutting performance, such as misalignment or irregularities when machining on multiple axes.
- Excess noise from the machine’s spindle motor could indicate an unstable speed output.
- Chipping along the edges of cutters due to overuse or inadequate lubrication leads to extra debris buildup in workpieces.
- A decrease in the machine’s overall performance.
Reduce Wear on Cutting Tools
You can reduce the wear on tools by using only quality cutting materials recommended for your particular task. Also, check if all of the parts are set up properly and kept in place securely to lessen vibration and improve accuracy.
Choose a suitable cutting speed depending on the material used; faster speeds will require tougher tooling but will aid in quicker production time. Be careful not to push too hard or fast, though! Additionally, ensuring sufficient coolant is provided throughout machining helps lubricate and prevent burning while removing heat from the system more effectively than dry-machining.
Consider using higher-grade carbide inserts where possible rather than less expensive options; they will last longer without becoming dull quickly due to frequent re-sharpening.
Strategies to Improve Quality
To reduce tool wear, keeping the cutting tools and other related equipment clean is a good practice. Dirt buildup on cutting edges can create bigger chips, which may increase machine vibration during operation. This, in turn, affects quality production in various ways.
Regular inspection of your machines is also important, as worn-out parts must be replaced before they cause serious damage or disruptions in operations. Moreover, proper lubrication should always be used for efficient machining since dry/poorly lubricated tools are prone to higher levels of friction that lead to greater chances for wear and tear, with decreased productivity rate too!
Tool wear is inevitable but not unavoidable. Proactive monitoring, observation, maintenance planning, good production practices, and accurate measurement techniques are the key to reducing tool wear and improving quality. Suncoast Precision Tools understands this concept, so they’re dedicated to providing superior machine tools and outstanding customer service for all your machining needs!
Their commitment to precision engineering excellence combined with a regular preventive maintenance program will help guarantee maximum performance from cutting tools while minimizing any potential tool degradation or premature failure down the line. Ensuring success in reducing tool wear requires dedication toward proper upkeep of machining operations. This leads us back to sustaining optimum results over time by investing in high-quality merchandise sourced through reliable suppliers like Suncoast Precision Tools!
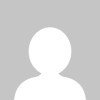