As companies scale or expand their product offerings, the need to be able to scale operating functions without crippling expense becomes vital. Modular Warehouse equipment—like adjustable pallet racking, mobile shelving units and configurable workstations—gives businesses the ability to rearrange their facilities quickly to meet changing needs. Additional racks and/or conveyors can be added and/or moved without much disruption for seasonal peaks or new product introductions. Likewise, Plastic crates are available in assorted shapes and sizes from ventilated plastic crates for perishables to heavy-duty molded plastic crates for industrial components. Standardizing crate dimensions and rack systems streamlines layout redesigns and minimizes the need for unique storage solutions. Such flexibility not only helps protect capital but also facilitates quick action in a favorable market.
Reusable plastic crates: Sustainability and cost savings
Sustainability is an acting aspect for contemporary enterprises. By replacing single-use packaging with reusable Plastic crates companies are helping to reduce waste and save money on packaging costs year on year. Although the initial expense of plastic crates is greater than that of cardboard, their longevity and resistance to wear and moisture make them much more economical over the long haul. In order to keep replacement costs down, as well, many organizations implement crate tracking programs that ensure assets stay within their supply chain. Additionally, plastic is recyclable at the end of its life, serving corporate sustainability goals and meeting regulatory requirements. Using green energy Warehouse equipment Melbourne, such as electric pallet trucks, as well as environmental-friendly lighting, can help reduce carbon footprints and utility costs, thereby improving both ecological credentials and the bottom line.
Improving efficiency by optimizing layout and flow
An efficient warehouse layout will be a crucial aspect of minimizing travel time and optimizing warehouse resources. Part of effective facility planning is to organize Warehouse machinery and storage areas according to inventory velocity, order profiles, and methods of handling. Fast movers need to be located close to packing and shipping stations to reduce picker walking distances, while less urgently moving stock can go into deeper rack locations. Dedicated lanes for the forklifts and AGVs help to manage the flow of traffic. Using Plastic crate with the correct volume helps to keep the item easily accessible while allowing organization and avoiding picking errors within flow racks or pick modules. Regular scoring of warehouse flows, supported through analytics built into WMS, can pinpoint bottlenecks and guide capital expenditures on more equipment or reconfigured layouts.
How To Calculate Return on Investment on Your Warehouse Equipment
The financial justification for every capital expense decision needs to be done. The ROI (return on investment) for new Warehouse is calculated by quantifying the cost savings from reduced overtime labor hours, reduced inventory shrinkage, or improved throughput. Raw metrics, like orders processed per hour, cost per order, and utilization of space before and after implementation supply hard proof that value has been created. The long term savings of the use of Plastic crates can also be seen by tracking the damage rates and replacement costs of storage media. It allows stakeholders to make informed decisions by providing scenario analyses that consider maintenance costs, equipment longevity, and depreciation. A strong ROI analysis not only will help to drive budget approvals, but will also help define performance baselines for continuous improvement initiatives.
Top Guidelines for Implementing New Systems for Your Warehouse Equipment
Incorporating new equipment into an active warehouse setting requires careful planning and communication. Site assessments should be performed by project teams to assess structural constraints, power requirements, and integration opportunities within current process. Engaging your frontline employees in equipment selection and layout design generates buy-in and reveals practical insights. All new pieces of machinery from forklifts to automated conveyors require ongoing and comprehensive training programs to be delivered in order to safely and efficiently operate the machinery. When it comes to storage solutions, standardizing around a small number of Plastic crates sizes can make it easier to handle materials and avoid confusion. This way the teams can take the time to put the equipment to the test, fine-tune the settings and workflows before actually leveraging it to its full potential. Lastly, by defining preventative maintenance schedules and observing performance metrics, we can ensure both the assets and crates perform efficient and sustainable.
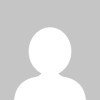