When choosing a medical contract manufacturer, having medical clean room assembly capabilities is very important for healthcare companies. The quality, rules, and care needed in the medical field need partners who get the balance between new technology and high-quality standards.
The Singapore Advantage in Medical Manufacturing
Singapore’s place as a world leader in biomedicine has important facts:
- Over 50 top biomedical science companies have set up manufacturing plants.
- The medical field uses over 13,000 skilled workers.
- Manufacturing of medical devices made over S$18.3 billion in 2023.
- 95% of Singapore’s medical tools are sent to markets worldwide.
Why Clean Room Manufacturing Makes the Difference
The stakes in making medical devices are very high. Every part must meet strict standards.
- ISO Class 7 clean rooms have less than 352,000 particles in each cubic metre.
- Keeping the temperature between ±0.5°C helps keep the material stable.
- Relative humidity kept at 55% ±5% stops problems with static electricity.
- Ongoing monitoring systems provide live environmental data.
Quality Systems That Exceed Global Standards
Modern medical manufacturing requires following several quality guidelines.
- ISO 13485:2016 certification is for managing the quality of medical devices.
- FDA 21 CFR Part 820 rules for getting into the US market
- The EU MDR 2017/745 is important for following the rules in Europe.
- HSA Singapore rules for following local laws and regulations
Advanced manufacturing technologies are changing how medical products are made.
Today’s medical contract manufacturers use advanced systems.
- Multi-axis CNC machining for complex geometries
- Metal injection molding for detailed, high-volume parts.
- Modern inspection systems with precision of 0.001mm.
- Automated assembly systems can lower the risk of human errors.
The Critical Role of Supply Chain Management
Statistics say that 63% of medical device recalls happen because of supplier quality problems. Top manufacturers deal with this by:
- Rigorous supplier qualification processes
- Real-time inventory tracking systems
- Several ways to source key parts
- Regular supplier audits and performance reviews
Cost-Effectiveness Without Compromise
Smart manufacturing methods bring strong money benefits:
- Automated processes can cut labor costs by as much as 40%.
- Lean manufacturing principles reduce waste by 25% to 30%.
- Just-in-time inventory reduces carrying costs
- Volume production economies of scale
Risk Management and Regulatory Compliance
According to Singapore’s Health Sciences Authority, making medical devices well needs:
- Comprehensive risk management systems
- Regular internal and external audits
- Documented validation processes
- Complete traceability of all components
Project Management Excellence
Making medical devices well needs careful project management.
- Dedicated project managers for each client
- Regular milestone reviews and updates
- Clear communication protocols
- Comprehensive documentation systems
The Future of Medical Manufacturing
Tomorrow’s manufacturing world is changed by new technologies.
- Industry 4.0 integration
- Artificial intelligence in quality control
- Advanced materials development
- Sustainable manufacturing practices
Making the Right Choice
When picking a manufacturing partner, think about these important factors:
- Technical capabilities and equipment
- Quality system maturity
- Regulatory compliance history
- Financial stability
- Communication systems
The busy world of making medical devices needs partners who know the technical needs and the rules in the industry. Top manufacturers, like AMT Pte Ltd, mix advanced manufacturing skills with good quality systems. This helps them do well in the contract manufacturing of medical devices.
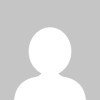